- Home
- Blog
- Plastic Polymer Composite Article
- What Are Plastic Fillers? The Application and Tips for Choosing the Right One
What Are Plastic Fillers? The Application and Tips for Choosing the Right One
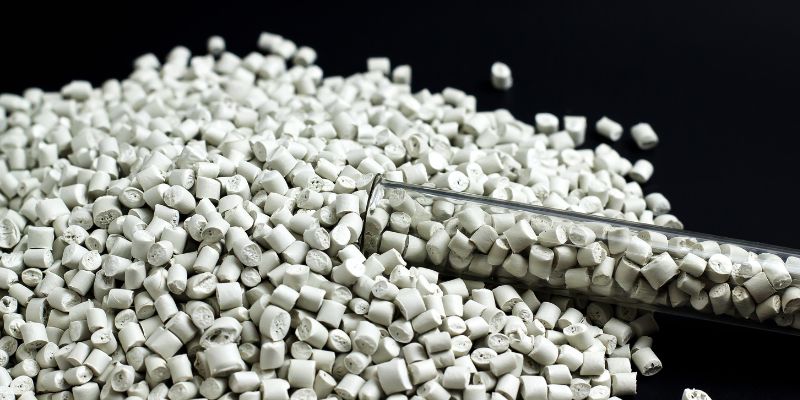
Plastic filler are common additives materials in modern industry, effectively enhancing strength, thermal resistance, used in major industries such as electronics, automotive, and packaging. Choosing the right plastic filler can not only reduce production costs but also make products more durable and ensure greater product quality. This article will provide an in-depth introduction to the types of plastic filler, their application industries, and key considerations when selecting a plastic filler, helping you find the most suitable materials.
What Are Plastic Fillers? What Benefits Do They Offer?
Plastic fillers are auxiliary materials added during the plastic manufacturing process, primarily used to enhance the rigidity, strength, thermal resistance, and stability of plastics, while also reducing production costs. Depending on their composition, plastic filler can be classified into two categories: inorganic fillers and organic fillers. Inorganic fillers such as calcium carbonate, talc powder, and barium sulfate are the most commonly used in the plastic industry due to their stable chemical properties and ease of processing.
What Types of Plastic Fillers Are There? You've Definitely Seen These Materials!
Calcium Carbonate
Calcium carbonate is currently one of the most common plastic fillers. Although a high filling ratio may affect the overall strength of the material, it can effectively enhance the tensile modulus of plastics, thereby increasing the material’s rigidity and density, which helps stabilize the product structure. In addition to improving physical properties, calcium carbonate can also increase the opacity and surface gloss of plastics, improve surface appearance, improve the impact resistance of the material, and serve as a processing aid to make the production process more efficient.
〈Extended Reading: What is Calcium Carbonate? A Comprehensive Guide to Its Production, Types, and Applications!〉
Talc Powder
Talc powder is mainly used as an additive in plastic materials such as polypropylene (PP), polyethylene (PE), and nylon (PA). It increases the rigidity of the materials, making plastic products more pressure-resistant and less prone to deformation during use. The addition of talc powder also significantly enhances the thermal resistance and dimensional stability of the plastic. Compared to virgin plastics, talc powder is more cost-effective, which not only reduces production costs but also maintains the necessary characteristics of the products. Therefore, it is commonly used in manufacturing processes such as injection molding, extrusion, and compression molding.
〈Extended Reading: Comprehensive Guide to Industrial-Grade Talc Powder:Properties and Advantages in Applications〉
〈Extended Reading: What Is Injection Molding? Applications, Processes, and Key Products Explained!〉
Barium Sulfate
Barium sulfate is an odorless, non-toxic inorganic compound that is insoluble in water. It can significantly enhance the density and durability of plastics, making the final products sturdier and giving them a heavier, more premium feel. In plastics such as polypropylene (PP) and polystyrene (PS), the filling ratio of barium sulfate can be as high as 70%, which not only effectively reduces production costs but also improves the acid and alkali resistance and light-blocking properties of the plastics. Additionally, because barium sulfate can effectively block X-rays, it is also commonly used in medical protective equipment and industrial radiation shielding materials.
Sodium Sulfate
Sodium sulfate is a white, non-toxic, odorless inorganic compound that is soluble in water. Due to its high transparency and low cost, it is often used as a plastic filler, making plastic products appear more transparent and glossy. Additionally, sodium sulfate can enhance the mechanical properties of the final product, such as good dispersion, high toughness, and excellent stability, ensuring the final product remains both visually appealing and mechanically robust.
Where Are Plastic Fillers Used? Discover the Two Main Application Areas!
Plastic fillers play an important role in modern manufacturing and can be found everywhere, from everyday consumer products to industrial components. Below are the two main areas where plastic fille is primarily used:
Plastic Filler Application 1: Automotive Industry
By adding different types of plastic filler, automotive parts can significantly reduce weight while maintaining strength and durability, thereby improving fuel efficiency and driving performance. Fillers such as talc powder, carbon black, and fiberglass are commonly used to manufacture lightweight components like bumpers, dashboards, and tires. These plastic fillers not only reduce the weight of automotive parts but also enhance strength and durability, ensuring stable performance of vehicles under various road conditions.
Application of Plastic Filler 2: Plastic and Rubber Industry
Plastic fillers are widely used to enhance the mechanical properties of both rubber and plastic, such as increasing hardness, wear resistance, and UV resistance. Therefore, they are commonly used in various products such as PVC pipes, plastic sheets, appliance housings, and cable conduits. Adding appropriate fillers not only extends the lifespan of these products but also enhances their stability in various environments.
How to Choose the Right Plastic Filler?
Each type of plastic filler has unique characteristics, and selection should be based on product requirements. By understanding these three key factors, you can avoid pitfalls and choose the right plastic filler!
1. Physical Properties
Different plastic products have different performance requirements, so it is essential to carefully evaluate whether the filler’s rigidity, density, and thermal resistance meet product requirements. For example, when manufacturing automotive parts or engineering plastics that require high hardness and wear resistance, it is advisable to choose fillers with higher rigidity. Selecting the right filler can not only enhance product quality but also extend the product's lifespan.
2. Chemical Compatibility
Plastic filler must be able to blend well with plastic materials to ensure that the product's stability and processing characteristics are not affected. Different plastics have varying compatibility with fillers; for example, calcium carbonate and talc are suitable for use in plastics like PP (polypropylene) and PE (polyethylene) due to their stable chemical structure. If the product requires higher weather resistance, barium sulfate is a good choice, as it offers excellent resistance to acids, alkalis, and weathering.
3. Filler Shape and Particle Size
The particle size and distribution of plastic filler can affect the processing flowability of plastics, the smoothness of the finished surface, and their physical properties. Fine particle fillers can make the plastic surface smoother and increase its transparency; larger particle fillers are more suitable for enhancing the rigidity and strength of products, such as structural components or products that must withstand higher mechanical loads. Additionally, a uniform distribution of filler particles can stabilize the internal structure of the plastic, achieving optimal results in both physical performance and appearance of the finished product.
Boost Your Product’s Competitiveness with Apex-VN Plastic Fillers!
Apex-VN is committed to the research and production of plastic fillers, with core products including calcium carbonate masterbatch, calcium carbonate, and talc powder. Apex-VN’s plastic fillers are widely used in applications such as blown film, extrusion, injection molding, and wire and cable, which not only enhance the rigidity and heat resistance of plastic products but also help lower production costs, providing the industry with efficient and stable solutions. In addition to economic benefits, quality remains one of Apex-VN’s greatest strengths. We have a stable supply of raw materials and implement strict quality control, ensuring that every step—from raw material selection to final production—is carefully monitored, providing customers with high-quality and reliable plastic filler.
〈Extended Reading: Full Guide to the Blown Film Process: From Plastic Pellets to Film Products for Industrial Applications〉
〈Extended Reading: A Comparative Study of PVC Compound and Masterbatch: Key Materials in Plastics Processing〉
Conclusion
As plastic products become increasingly prevalent across various industries, choosing the right plastic filler can not only enhance product performance but also effectively reduce production costs. By understanding the characteristics of different plastic fillers, companies can optimize their production processes and create more competitive products. Apex-VN offers stable, high-quality plastic fillers, providing efficient and reliable solutions for various industries. Looking for a high-quality plastic filler? Contact us today to find the ideal solution for your needs!
〈Extended Reading: What is Extrusion? Principles, Applications, and Its Benefits for Long Plastic Products〉
Article Classification
Recent Articles
- A Complete Guide to Polypropylene (PP): Properties and Applications
- What Is PE Plastic? A Complete Guide to Its Types, Properties, Advantages, and Applications
- What Are Plastic Fillers? The Application and Tips for Choosing the Right One
- Full Guide to the Blown Film Process: From Plastic Pellets to Film Products for Industrial Applications
- What Is Injection Molding? Applications, Processes, and Key Products Explained!