A Comprehensive Overview of APEX's QC System
Introduction of APEX's QC System
With the rapid development of industries such as construction, plastics, and rubber, there is a growing demand for high-quality calcium carbonate masterbatch and calcium carbonate powder. APEX, as a professional masterbatch manufacturer, is committed to providing excellent quality products to meet the expanding market demand. In this competitive industry, APEX upholds high-quality standards and ensures exceptional quality throughout the production process with its QC System, offering reliable masterbatch solutions to customers.
Basic Principles of the QC System
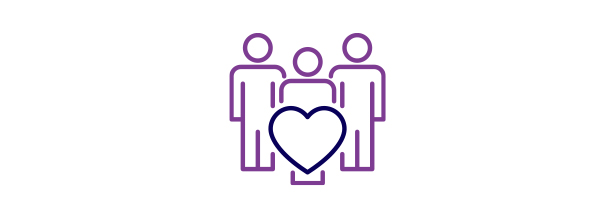
A. Customer-Oriented Approach
APEX QC System focuses on a customer-oriented approach. We prioritize customer needs by actively listening to feedback and expectations. This approach ensures that our calcium carbonate masterbatch and powder meet all application requirements..
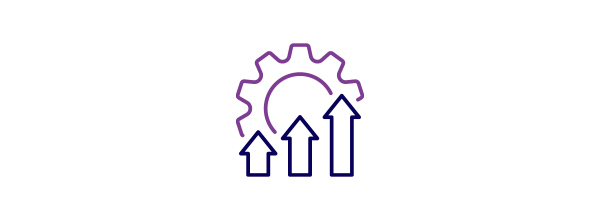
B. Continuous Improvement
Continuous improvement is key to the APEX QC System. We regularly review and optimize production processes to boost efficiency, cut costs, and enhance the quality of our calcium carbonate products. This drives our commitment to excellence.

C. Data and Fact-Based Approach
APEX QC System relies on a data and fact-based approach. We use advanced testing and analysis to gather accurate data, ensuring that every batch of calcium carbonate products meets high-quality standards.
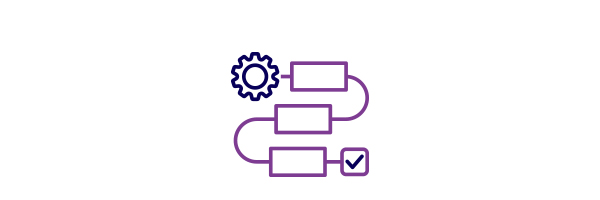
D. Involvement of Decision-Makers and Leadership
Leadership involvement is crucial in the APEX QC System. Active participation from decision-makers ensures QC goals align with company objectives, driving effective implementation of quality management practices.
Implementation Steps of the QC System
A. In-House Quality Control Inspection (4 Stages)
(1) Incoming Material Inspection
(2) In-Process Quality Control Inspection
(3) Finished Product Quality Inspection
(4) Production Analysis Inspection (COA)
.jpg)
Quality Control Inspection in accordance with International Standards
- RoHS Compliance Testing: Refer to IEC 62321:2008
- Heavy Metals Testing: EN71-3 or ASTM-F963
- Specific Surface Area (BET): ASTM D3663-2003
- Tensile Testing: ASTM D412 JIS-k6251, JIS-k6252
- Purity Testing: CNS 1625 (Analysis according to CNS1625 method [HCl titration])
- Oil Absorption Measurement: JIS-K5101
- Loss on Ignition: JIS-K5101
- pH: JIS-K5101
- Wet Sieving Method: CNS 13567 K0057
Example using PVC Compound
Inspection Process:
Raw Material Inspection for PVC -> In-process Inspection for PVC Manufacturing -> Process Control for PVC Manufacturing
PVC Raw Material Inspection
(1) PVC powder and other powdered substances
- Fish-eye test
- Particle size distribution test
- Transparency check
(2) Liquid substances
- Specific gravity
- Volatility
In-process Inspection of PVC
Sampling 500g every 30 minutes
- Specific gravity
- Hardness
- Color difference
- Gelation degree
- Sheet extrusion trial
Control in PVC Manufacturing
- Automated computer-controlled measurement to minimize human errors.
- Design of enclosed spaces in conveyor pipelines to prevent powder leakage.
- Reduction in powder occurrence and effective prevention of spillage.
B. Outsourced Qualified Laboratory Testing
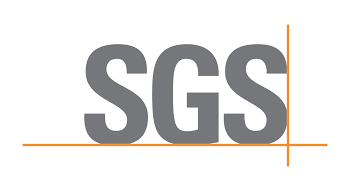
Advantages and Challenges of the QC System
Advantages
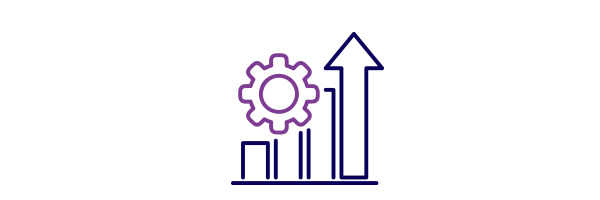
Enhanced Product Quality:
The QC system ensures consistent production, reducing defects and meeting customer expectations.
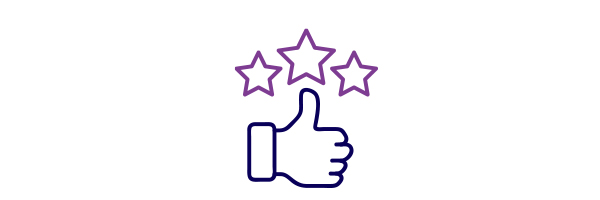
Increased Customer Satisfaction:
Stable product quality builds trust, customer loyalty, and positive word-of-mouth.
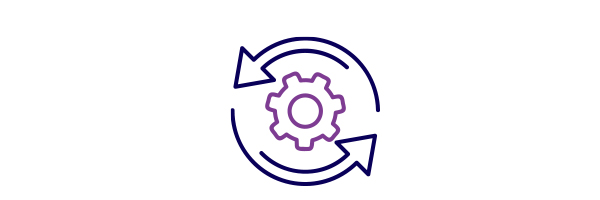
Improved Production Efficiency:
QC reduces errors and delays, improving efficiency, lowering costs, and speeding time to market.
Challenges
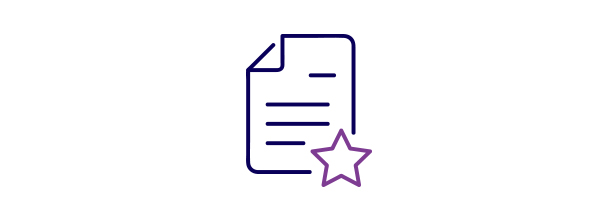
Implementation and Execution Difficulty:
Setting up a QC system requires significant resources, including staff training, equipment, and procedures, posing cost and execution challenges.
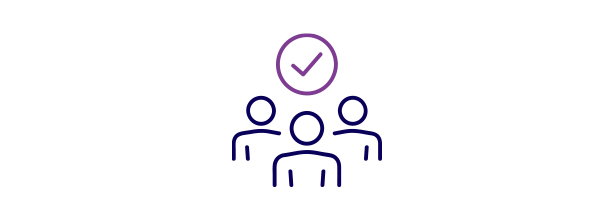
Continuous Improvement Challenges:
Maintaining ongoing quality improvement demands continuous effort, resources, and adaptation to market and technological changes.
Conclusion
Summary of the Importance of the QC System
In summary, the QC system is essential for the success of a company. It not only ensures consistency and reliability in product quality, enhances customer satisfaction, but also improves production efficiency, reduces costs, and strengthens competitiveness. Through effective implementation and execution of the QC system, companies can establish a positive brand image, gain customer trust, and achieve sustainable development.
Future Development Outlook
Looking ahead, we will continue to focus on improving and innovating our QC system to meet the evolving market demands and technological challenges. We will further strengthen customer orientation, enhance communication and cooperation with customers to ensure our products fully meet their needs and expectations. At the same time, we will continue to invest in talent training and technology research and development to continuously improve our production capabilities and quality standards, thus achieving sustainable development and growth for the company.