- Home
- Blog
- Powders Article
- What is Calcium Carbonate? A Comprehensive Guide to Its Production, Types, and Applications!
What is Calcium Carbonate? A Comprehensive Guide to Its Production, Types, and Applications!
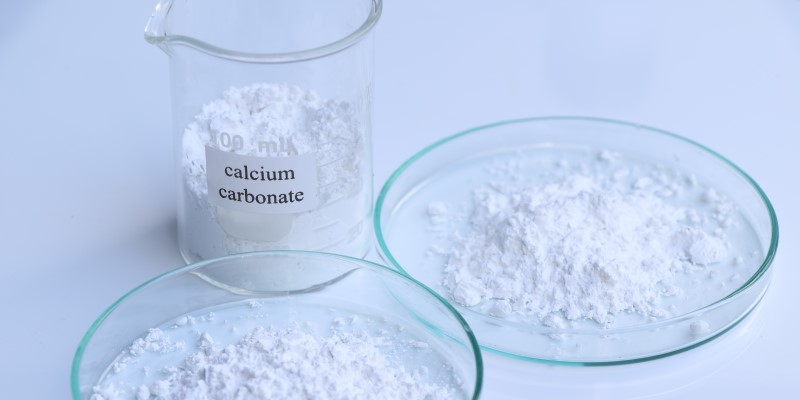
Calcium carbonate is a common mineral found naturally in rocks, sediment layers, and groundwater. Its applications span across numerous industries, including paper manufacturing, rubber, building materials, plastics production, paints, food additives, and agriculture. This article delves into the various types of calcium carbonate and its industrial applications, providing a comprehensive overview of its significance in modern industries!
What is Calcium Carbonate?
Calcium Carbonate (CaCO₃) is a chemical compound that occurs naturally and is also produced synthetically. In nature, calcium carbonate is primarily found in limestone, marble, shells, and other sedimentary rocks. Synthetic calcium carbonate is produced through chemical processes using limestone as a primary source. This inorganic compound is highly significant in industrial and manufacturing sectors and is one of the most used fillers!
Calcium carbonate typically appears as a white powder or granule. While it has low solubility in water, it readily dissolves in acids like hydrochloric acid, producing carbon dioxide, water, and a soluble calcium salt. When heated above 825°C, calcium carbonate decomposes into calcium oxide (CaO) and carbon dioxide (CO₂). Calcium carbonate can be used as a standalone reinforcing filler or in combination with other fillers such as carbon black, silica, clay, and titanium dioxide, acting as a semi-reinforcing filler, colorant, or extender to improve processing and product characteristics. Additionally, calcium carbonate can effectively reduce rubber content or replace expensive white fillers, resulting in more cost-effective products.
<Extended Reading: What is Filler Masterbatch? Explanation of the Filler Masterbatch Process and the Applications of Calcium Carbonate Masterbatch>
Introduction to Calcium Carbonate Production Process
Most of the calcium carbonate used in industry is extracted from mining or quarrying. Pure calcium carbonate intended for food or pharmaceutical use is typically produced from pure quarry sources, such as marble. Currently, industrial production of ground calcium carbonate (GCC) primarily uses two methods: dry and wet processing. The dry process is mainly applied in industries like rubber, plastics, and coatings, while the wet process is more suited to the paper industry. Below is a detailed introduction to the most common dry production methods on the market:
Calcium Carbonate Processing and Equipment
In the production of ground calcium carbonate (GCC) powder, the dry grinding process is widely used due to its simplicity and shorter process flow, as it does not require additional filtering, drying, or other dewatering steps. This process is easy to operate, simple to control, and involves lower investment costs, with relatively inexpensive operating expenses. The primary processing stages include crushing, grinding, and classification, and commonly used equipment includes impact mills, Raymond mills, air flow mills, and ball mills.
Configuration of Calcium Carbonate Production Lines
In addition to ultrafine mills with built-in classifiers, equipment like impeller-type classifiers is commonly configured on production lines to ensure product fineness and particle size distribution. These devices are available in two setups: internal and external. The internal configuration operates in a closed-loop production mode, while the external configuration can be used in either open or closed-loop modes. The open-loop system can produce two products with different fineness levels, whereas the closed-loop system is dedicated to producing a single ultra-fine powder.
Particle Size in Calcium Carbonate Production
Different grinding equipment produces products with varying levels of fineness. Generally, the dry process is better suited for producing coarser ground calcium carbonate (GCC) products. Raymond mills can produce GCC with particle sizes ranging from 38 to 74 μm. If a dry fine classifier is incorporated into the production process, it is possible to produce GCC with particle sizes of 10 μm, 18 μm, and 25 μm. Although ultra-fine grinding equipment combined with classifiers requires significant investment and has higher energy consumption, it can produce GCC with particle sizes below 10 μm, making them suitable as high-end fillers in industries such as plastics and rubber.
<Extended Reading: A Comparative Study of PVC Compound and Masterbatch: Key Materials in Plastics Processing>
What are the Types of Calcium Carbonate?
Depending on the grinding principles used in production, calcium carbonate can exhibit different particle shapes, each with unique physical and chemical properties. The four common types of calcium carbonate available on the market are: ground calcium carbonate (GCC), precipitated calcium carbonate (PCC), activated calcium carbonate, and nano calcium carbonate. Each type is suited to different industrial applications and product requirements.
Ground Calcium Carbonate (GCC)
Ground calcium carbonate (GCC) is a finely milled high-purity calcium carbonate powder. Its main characteristics include high fineness, high whiteness, and high density. Finely processed GCC exhibits excellent whiteness and relatively high bulk density due to the grinding process. The particle size of ground calcium carbonate typically ranges between 2 to 10 microns, giving it a large specific surface area. GCC is widely used in various industrial and everyday applications.
Precipitated Calcium Carbonate (PCC)
Precipitated calcium carbonate (PCC) is produced through chemical synthesis or vapor deposition processes, resulting in a lower density and specific particle size. Compared to ground calcium carbonate (GCC), PCC has a lower density. Key characteristics include smaller particle sizes, typically ranging from 0.5 to 5 microns, which provide a larger specific surface area (SSA). This property enhances its flowability in applications such as the plastics industry, rubber manufacturing, paints, coatings, and the paper industry. Additionally, finely processed PCC usually has high whiteness, improving the aesthetic quality of the final products.
Activated Calcium Carbonate
Activated calcium carbonate (ACC) is a specially treated form of calcium carbonate, enhanced through chemical or physical methods to increase its reactivity and specific surface area, allowing it to participate more effectively in chemical reactions. This surface treatment powder typically has a particle size ranging from 0.5 to 2 micrometers, characterized by a uniform particle size distribution and high specific surface area. These properties enhance filler dispersion and improve processing performance. Its low moisture content and insolubility in hydrochloric acid (HCl) ensure product stability and durability. The surfactants present on the surface enable better bonding with other materials, further enhancing the overall performance and reliability of the product.
Nano Precipitated Calcium Carbonate
Nano Precipitated Calcium Carbonate is a form of calcium carbonate with nano-scale particle sizes, typically ranging from 1 to 100 nanometers. Due to its extremely small particle size, Nano Precipitated Calcium Carbonate usually exhibits excellent transparency, making it suitable for applications requiring a transparent effect. This material is produced through specialized synthesis or processing techniques and has much smaller particle sizes than traditional calcium carbonate, along with unique physical and chemical properties. It can disperse uniformly in liquid or solid media and is resistant to sedimentation. Furthermore, Nano Precipitated Calcium Carbonate offers superior reinforcing properties, allowing for a 30% to 50% increase in filler loading, thereby reducing costs.
Differences Between Four Types of Calcium Carbonate
|
Ground Calcium Carbonate |
Precipitated Calcium Carbonate |
Activated Calcium Carbonate |
Nano Precipitated Calcium Carbonate |
---|---|---|---|---|
Raw Materials Used |
Natural limestone blocks |
Natural limestone blocks |
Natural limestone blocks, |
Natural limestone, |
Particle Size |
2~10 microns |
0.5~5 microns |
0.5~2 microns |
1~100 nanometers |
Features |
High fineness, |
Small particle size, |
Uniform particle size distribution, |
Volume filling, |
Industrial Applications of Calcium Carbonate
Calcium carbonate is widely and diversely applied across various industries, playing a key role in enhancing product performance, reducing costs, and improving processing efficiency. Selecting the appropriate grade of calcium carbonate based on specific needs can achieve optimal results. Below, we will introduce the common characteristics of calcium carbonate as a filler material and explore its applications in different industries.
Rubber Industry
In the rubber industry, calcium carbonate can enhance the hardness, wear resistance, and tensile strength of tires. It also improves the wear resistance and anti-aging properties of seals and gaskets, while increasing the pressure resistance and service life of rubber hoses and belts. Common products include tires, seals, gaskets, rubber hoses, and belts.
Plastic Manufacturing
Calcium carbonate improves the rigidity and durability of PVC products while reducing costs. In PE and PP products, it enhances hardness and dimensional stability. For engineering plastics like ABS and PA, it boosts heat resistance and mechanical strength. In plastic films, calcium carbonate increases hardness, puncture resistance, and transparency. Common products include PVC pipes, PVC sheets, PE and PP products, ABS and PA plastics, and plastic films.
<Extended Reading: The Application of Calcium Carbonate Masterbatch in the Plastic Bag Industry >
<Extended Reading: Application of Calcium Carbonate Masterbatch in the PE Buffer Packaging Material Industry>
Paints and Coatings
In architectural coatings, calcium carbonate improves coverage and weather resistance; in industrial coatings, it provides abrasion resistance and chemical durability; in automotive coatings, it enhances the hardness and gloss of the paint film; and in wood coatings, it increases hardness and wear resistance. Common products include interior and exterior wall paints, protective coatings, automotive paints, and wood coatings.
Agriculture and Livestock
conditioner, feed additive, and pesticide carrier. It improves soil quality, enhances crop growth, and provides nutrients while protecting plants. In livestock farming, calcium carbonate is mainly used as a feed additive and bedding material, providing essential calcium nutrition, improving animal health, and boosting production performance.
<Extended Reading: The application of Calcium Carbonate Masterbatch in Agricultural Mulch Film>
Food Additive
Calcium carbonate has wide and diverse applications as a food additive. It not only provides calcium nutrition but also regulates food acidity, prevents caking, and improves texture. In the pharmaceutical field, calcium carbonate is also widely used, offering calcium supplementation, relieving excessive stomach acid, enhancing drug stability, and serving as an excipient in drug formulations.
(APEX's calcium carbonate is limited to industrial-grade use only and is not currently available for pharmaceutical-grade applications.)
FAQ About Calcium Carbonate
Before deciding on large-scale production of calcium carbonate powder, it is crucial to consider the following key factors to ensure that the selected product meets your specific requirements. These critical factors include the fineness, purity, and particle size distribution of calcium carbonate, as well as its suitability for specific applications.
Q1: What Are the Key Factors That Affect the Quality of Calcium Carbonate Powder?
The quality of calcium carbonate powder is influenced by several factors, including the purity of the raw materials, particle size, and grinding process. The calcium content in the powder must meet standard requirements, and impurities in the raw materials such as magnesium, iron, and aluminum should be avoided, as they can affect the color and performance of the powder. The particle size and shape of the raw materials play an important role in the grinding process and the final particle size distribution. Selecting the appropriate grinding technology, such as vertical milling machine or ball mills, is crucial for achieving high-quality powder. Additionally, pre-treatment of the raw materials (e.g., cleaning and drying) and post-treatment (e.g., surface modification and coating) also impact the final product's performance. Lastly, proper storage and environmental control of the raw materials help ensure the stability of the calcium carbonate powder's quality.
Q2: What Should I Consider for Quick Delivery of Calcium Carbonate Products?
To expedite the delivery of calcium carbonate, it is essential to consider the supplier's packaging technology and inventory management. Opting for a manufacturer equipped with a semi-automated filling and packaging area can significantly enhance packaging speed and reduce human error. More advanced suppliers may also have robotic palletizing systems that accelerate finished product stacking, shorten order fulfillment time, and ensure prompt delivery.
Q3: How Many Grades of Industrial Calcium Carbonate Can Be Classified According to Different Degrees of Fineness?
Industrial-grade calcium carbonate can be classified into different grades based on "particle size, purity, application, and surface treatment." Different industries require varying specifications of calcium carbonate to meet specific performance requirements and cost considerations. Therefore, selecting the appropriate grade is crucial. Below are some common classification methods:
Based on particle size:
-
Fine Calcium Carbonate : Particle size is typically less than 1 micron (μm), also known as nano calcium carbonate.
-
Microfine Calcium Carbonate : Particle size is usually between 1 and 5 microns (μm).
-
Regular Calcium Carbonate : Particle size is usually between 5 and 45 micrometers (μm).
-
Coarse Calcium Carbonate : Particle size is typically greater than 45 microns (μm).
Based on purity and application:
-
Precipitated Calcium Carbonate (PCC) : Known for its high purity and consistent particle size distribution, it is commonly used in high-end applications such as pharmaceuticals, food, cosmetics, and plastic fillers.
-
Ground Calcium Carbonate (GCC) : Obtained from natural limestone through mechanical processing, GCC generally has lower purity and a less uniform particle size distribution compared to PCC. However, it is more cost-effective and widely used in construction materials, paints, rubber, and papermaking industries.
Based on surface treatment:
-
Surface-treated Calcium Carbonate : This is calcium carbonate whose surface properties have been altered through chemical treatments, improving its performance in specific applications such as plastics and rubber, enhancing its dispersibility and compatibility
-
Untreated Calcium Carbonate : This refers to calcium carbonate that has not undergone any surface treatment and thus retains its original physical and chemical properties.
Q4: What Is the Difference Between Precipitated Calcium Carbonate (PCC) and Ground Calcium Carbonate (GCC)?
Precipitated calcium carbonate (PCC) and ground calcium carbonate (GCC) are the two most common types of calcium carbonate available on the market. Their main differences lie in particle size, shape, density, and specific surface area. PCC has finer particles, with an average size usually less than 1 micron (μm), and its particle shapes vary, including spherical, needle-like, or cubic. It has a lower density, typically around 2.4 to 2.7 g/cm³, and a larger specific surface area, providing better dispersibility and adsorption properties. In contrast, GCC has larger particles, with an average size ranging between 1 and 45 microns (μm). The particle shapes are more irregular, and it has a higher density, usually between 2.7 and 2.9 g/cm³, with a smaller specific surface area. These differences affect their performance in different applications.
Conclusion
APEX offers a wide range of calcium carbonate products, using natural limestone from Vietnam as raw material to ensure product quality and meet various customer needs. Our calcium carbonate powder features fine particle sizes, high specific surface area, and low bulk density, making it more convenient for processing and transportation. Additionally, our products boast high whiteness and low residue, enhancing the appearance and texture of end products. APEX's Ultra-fine Calcium Carbonate is finer than other brands, making it especially suitable for the plastics and paint manufacturing industries. If you'd like to learn more about the calcium carbonate products that are best suited for your industry, feel free to contact us, and our specialists will provide product consultation services.